System MES (Manufacturing Execution System) to oprogramowanie wspierające zarządzanie produkcją w czasie niemal rzeczywistym. Łączy dane z maszyn, procesów i rejestracji ręcznej przez pracowników, eliminując papierową dokumentację, poprawiając efektywność i jakość. System MES umożliwia m.in.:
- Monitorowanie wydajności produkcji (z wykorzystaniem m.in. OEE, a więc wskaźnika opisującego całkowitą efektywność wyposażenia).
- Kontrolę realizacji produkcji, poprzez dostarczenie odpowiednich informacji na terminal oraz rejestrację wszystkich niezbędnych danych.
- Dostęp do raportów i analiz, które są nieocenionym wsparciem w inicjatywach takich jak Lean Manufacturing czy Continuous Improvement.
- Zaawansowane integracje z innymi systemami firmy produkcyjnej czy akwizycję danych z maszyn.
W rezultacie, oprogramowanie klasy MES pomaga optymalizować produkcję i dostarcza wszystkich niezbędnych narzędzi do poprawnej realizacji procesu. W Operator Systems mamy ponad 20 lat doświadczenia w tworzeniu wdrażaniu takich rozwiązań. W tym artykule podzielimy się z Tobą naszą wiedzą i przemyśleniami na temat systemów MES.
Co to jest system MES?
Skrót MES oznacza, z angielskiego, Manufacturing Execution System – a więc „System Realizacji Produkcji”. Jest to klasa rozwiązań wspierających zarządzanie produkcją, które według standardu ISA-95 mają za zadanie integrować poziom biznesowy w przedsiębiorstwie (ERP – Enterprise Resource Planning) z halą produkcyjną (maszyna, system SCADA, pracownik).

W praktyce – system MES bywa nazywany „mózgiem” firmy produkcyjnej. Dzięki niemu firma wie, co, kiedy i jak zostało wyprodukowane. System ten dostarcza produkcji zadania (co, w jakiej kolejności, w jaki sposób należy wyprodukować), zbiera dane z maszyn (automatycznie) i stanowisk pracy (za pomocą intuicyjnych, prostych ekranów), monitoruje postępy produkcji, analizuje wydajność oraz pomaga szybko wykrywać i rozwiązywać problemy, takie jak opóźnienia czy awarie.
Początki historii systemów MES sięgają lat 70., kiedy rozwijano systemy do monitorowania maszyn, które z czasem ewoluowały w zaawansowane narzędzia wspierające Lean Manufacturing i cyfryzację produkcji. Z czasem do zakresu dodawane były kolejne obszary funkcjonalne, takie jak logistyka produkcji, kontrola jakości, etc… Obecnie przyjmuje się, że dobry system klasy MES powinien mieć wszystkie narzędzia potrzebne na produkcji – tak, aby pracownicy mogli uzyskać niezbędne informacje i zarejestrować zdarzenia przy użyciu jednej aplikacji.
Zaawansowane systemy MES często wykorzystują również nowoczesne technologie, takie jak IIoT (Industrial Internet of Things) oraz systemy BI (Business Intelligence) służące do zaawansowanej analizy danych. W rezultacie umożliwiają np. dokładne śledzenie wskaźników OEE w oparciu o dane z maszyn czy analizę przyczyn powstawania problemów. Jeśli chcesz poznać kierunek w którym naszym zdaniem zmierza ewolucja systemu MES przyglądamy się temu zagadnieniu w dalszej części artykułu – „Przyszłość systemów MES”.
Choć czasem utożsamiany systemy MES z MOM (Manufacturing Operations Management), MES skupia się na operacyjnej stronie produkcji, stanowiąc kluczowy element strategii optymalizacji procesów w przedsiębiorstwach produkcyjnych.
Spis Treści
Funkcje i możliwości systemów MES
Zakres funkcjonalny systemów klasy MES powinien, tak jak wspominaliśmy powyżej, obejmować wszystkie narzędzia niezbędne dla produkcji. W rezultacie – precyzyjne zdefiniowanie funkcjonalności tej klasy systemów jest niemałym wyzwaniem.
Standard MESA-11 (MESA International)
Podstawowym zestawieniem funkcjonalności MES, do którego odwołuje się wiele artykułów i specyfikacji jest tzw. MESA-11, a więc model rozwiązań klasy rozwiązań MES zaproponowany przez MESA International w 1996 roku. MESA International to globalna organizacja non-profit, która wspiera rozwój technologii i standardów w obszarze zarządzania produkcją, łącząc systemy IT i operacyjne w celu poprawy efektywności procesów w przemyśle. Oryginalna lista MESA-11 wygląda następująco:
- Operations/detailed Scheduling – Harmonogramowanie operacyjne zadań
- Resource Allocation & Status – przypisanie pracy do zasobów oraz informacja o ich statusie
- Performance Analysis – ocena efektywności produkcji
- Dispatching Production Units – dyspozycja (przekazanie) zadań na produkcję
- Product Tracking & Genealogy – śledzenie statusu produkcji oraz genealogii (tzw. traceability)
- Labor Management – zarządzanie personelem
- Quality Management – zarządzanie jakością
- Data Collection – zbieranie danych np. z maszyn
- Process Management – zarządzanie procesem produkcji
- Maintenance Management – zarządzanie utrzymaniem ruchu
- Document Control – zarządzanie dokumentacją
Od roku 1996 naturalnie wiele się zmieniło w specyfikacji systemów MES, a sama MESA International aktualizowała swoje modele i podejście do tej klasy systemów kilka razy (w 2004 powstał model C-MES, 2008 – Strategic Initiatives, 2022 – Smart Manufacturing).
Funkcjonalności systemów MES w praktyce
W praktyce – zakres funkcjonalności oferowanych systemów MES może różnić się w zależności od dostawcy oraz specyfiki produkcji klienta.
Każdy producent oprogramowania interpretuje wymagania wobec systemów MES nieco inaczej, dostosowując swój produkt do specyfiki branż, które obsługuje i wymagań użytkowników. Wiele systemów MES wywodzi się z konkretnej, jednej funkcjonalności – np. monitorowania efektywności procesu. W rezultacie, część obszarów jest bardziej zaawansowana, a niektóre dostarczają tylko podstawowych funkcjonalności.
Firmy produkcyjne również często wybierają jedynie te moduły, które odpowiadają ich aktualnym potrzebom. W praktyce niewiele systemów oferuje pełen zakres funkcjonalności na najwyższym poziomie, dlatego kluczowe jest dopasowanie rozwiązania do konkretnej organizacji i jej celów biznesowych.
Warto również zauważyć, że wymagania wobec systemów MES stale ewoluują, a wraz z rozwojem technologii pojawiają się nowe oczekiwania i funkcjonalności. Z tego powodu lista funkcji systemu MES którą proponujemy poniżej nie jest „definitywna” i może różnić się w zależności od kontekstu wdrożenia czy dostawcy.
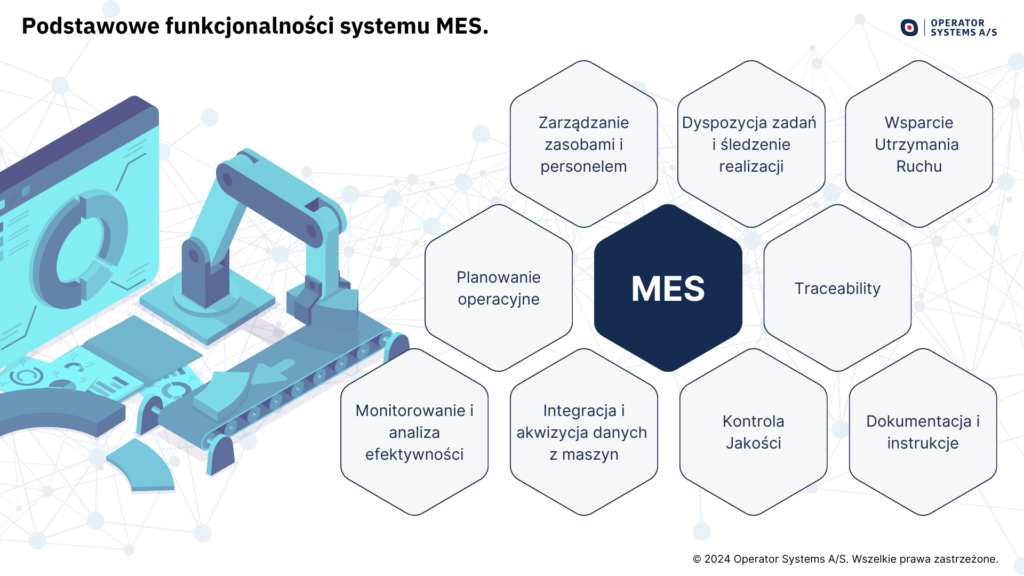
Do głównych funkcji systemu MES które należy brać pod uwagę w 2025 roku należą:
1. Monitorowanie produkcji w czasie rzeczywistym
System MES umożliwia bieżące śledzenie procesów produkcyjnych, zapewniając pełną widoczność stanu maszyn, realizacji zleceń i wydajności produkcji. Wyniki mogą być wyświetlane np. na dużych ekranach widocznych na produkcji, dzięki czemu wszyscy znają jej aktualny stan. Dzięki temu możliwa jest natychmiastowa reakcja na odchylenia od planu, co minimalizuje straty i przestoje.
2. Kontrola jakości
MES gromadzi dane jakościowe z procesu produkcyjnego, automatycznie analizuje odchylenia od norm i generuje raporty oraz powiadomienia/alerty. To pozwala na szybkie wykrywanie problemów i wdrażanie działań naprawczych, a w rezultacie – na podnoszenie jakości produkcji.
3. Planowanie i harmonogramowanie
W systemach MES funkcjonalności związane z planowaniem i harmonogramowaniem zadań produkcyjnych najczęściej koncentrują się na wsparciu operacyjnym, a nie na pełnym procesie strategicznego planowania i szczegółowego harmonogramowania produkcji z uwzględnieniem ograniczonych zasobów (tak, jak robią to np. systemy klasy APS). MES pomaga użytkownikom w ustaleniu sekwencji zadań, priorytetów oraz właściwej kolejki na produkcję, bazując na danych dostępnych w czasie rzeczywistym, takich jak dostępność maszyn, surowców czy stan pracowników.
4. Śledzenie i identyfikowalność (traceability)
Rozwiązanie klasy MES umożliwia śledzenie każdego produktu i jego komponentów na wszystkich etapach produkcji. Zapewnia to pełną identyfikowalność (a więc traceability zarówno procesowe jak i materiałowe), co jest kluczowe dla spełnienia wymagań regulacyjnych oraz zarządzania reklamacjami i zwrotami. Pomaga także znacząco ogranicza koszty i zakres działań związanych z zarządzaniem problemami jakościowymi, takimi jak wycofanie produktów z rynku (callback) czy kwarantanna wadliwych partii.
5. Zarządzanie zasobami
System monitoruje dostępność i stan maszyn, urządzeń oraz materiałów. Pozwala to na lepsze planowanie produkcji, unikanie opóźnień wynikających z braku surowców i optymalizację wykorzystania sprzętu.
6. Zarządzanie dokumentacją
System MES może zarówno przechowywać dokumentację techniczną, instrukcje pracy i procedury, jak i integrować się z dedykowanymi systemami, takimi jak PDM/PLM czy folderami sieciowymi. Choć przechowywanie dokumentów bezpośrednio w MES jest możliwe, bardziej efektywnym rozwiązaniem jest integracja z istniejącymi źródłami, co zapewnia dostęp do zawsze aktualnych i centralnie zarządzanych danych. Dzięki temu pracownicy mogą łatwo znaleźć potrzebne informacje, minimalizując ryzyko błędów i wspierając spójność procesów produkcyjnych.
7. Analiza wydajności
Kluczową funkcjonalnością systemu MES jest śledzenie wskaźników takich jak OEE (Overall Equipment Effectiveness) i TEEP (Total Effective Equipment Performance), dostarczając kompleksowego obrazu efektywności produkcji. OEE ocenia dostępność, wydajność i jakość, natomiast TEEP uwzględnia całkowity dostępny czas, co pozwala na pełniejszą ocenę wykorzystania zasobów.
System analizuje zarówno bieżące dane w czasie rzeczywistym, jak i długoterminowe trendy, identyfikując obszary do poprawy. MES wspiera analizę przyczyn problemów (Root Cause Analysis), prognozowanie wydajności i porównanie kluczowych wskaźników, umożliwiając wdrażanie skutecznych działań optymalizacyjnych.
8. Zarządzanie przestojami
Rozwiązanie MES efektywnie wspiera zarządzanie przestojami, rejestrując szczegółowe informacje o ich wystąpieniu, czasie trwania oraz przyczynach. System umożliwia przypisywanie kodów przyczyn przestojów, które mogą być zdefiniowane według standardowych kategorii (np. awaria maszyny, brak materiałów, przerwa konserwacyjna) lub dostosowane do specyfiki zakładu. Dane te są następnie wykorzystywane do analizy, na przykład przy użyciu diagramu Pareto, co pozwala zidentyfikować główne źródła problemów i priorytetowość działania naprawcze.
MES może również rejestrować przyczyny pracy z obniżoną efektywnością, np. zmniejszonej prędkości maszyny czy pogorszenia jakości surowców. Dzięki temu możliwe jest dokładne śledzenie strat w produkcji nie tylko w wyniku pełnych przestojów, ale także w trakcie nieoptymalnego działania procesów.
Funkcjonalności te wspierają nie tylko szybkie reagowanie na bieżące problemy, ale również długoterminową optymalizację.
9. Integracja z innymi systemami
MES łączy warstwę zarządzania biznesowego z operacyjną, integrując się z innymi systemami w przedsiębiorstwie i zbierając dane bezpośrednio z maszyn. Taka architektura umożliwia płynną wymianę informacji oraz zapewnia pełną widoczność procesów produkcyjnych.
Integracja z innymi systemami IT
MES współpracuje z wieloma systemami informatycznymi występującymi w firmach produkcyjnych, jak np. ERP, APS, WMS czy SCADA, ułatwiając synchronizację danych między różnymi obszarami przedsiębiorstwa. Integracja pozwala na spójne zarządzanie produkcją, od planowania strategicznego po operacyjną realizację zadań. Dzięki temu dane o zleceniach, harmonogramach czy materiałach są na bieżąco aktualizowane i dostępne dla wszystkich użytkowników.
Akwizycja danych z maszyn
MES zbiera dane z urządzeń produkcyjnych w czasie niemal rzeczywistym, obejmujące stan maszyn, parametry procesów oraz wyniki produkcji. Informacje te są wykorzystywane do monitorowania efektywności, identyfikowania problemów i optymalizacji działań. Bezpośrednie połączenie z maszynami pozwala również na szybkie reagowanie na awarie i odchylenia, co wspiera ciągłość produkcji.
10. Zarządzanie pracownikami
System MES umożliwia kompleksowe zarządzanie pracą personelu na hali produkcyjnej, rejestrując czas pracy i monitorując wydajność pracowników. Dzięki temu menedżerowie mają pełny wgląd w zaangażowanie zespołów, co pozwala na lepsze planowanie pracy, optymalne alokowanie zasobów oraz szybkie reagowanie na braki kadrowe lub opóźnienia.
Dodatkowo MES umożliwia szczegółowe śledzenie kosztów robocizny przypisanych do poszczególnych zleceń produkcyjnych. Dane te pozwalają na precyzyjną analizę opłacalności zadań oraz identyfikację obszarów, gdzie można wprowadzić optymalizacje. Takie funkcjonalności wspierają również działania motywacyjne, ponieważ przejrzystość wyników i wydajności pracy pozwala na obiektywną ocenę i nagradzanie pracowników za ich wkład w realizację celów produkcyjnych.
11. Monitorowanie parametrów procesu i zgodności z technologią
Rozwiązanie MES zapewnia bieżące monitorowanie kluczowych parametrów procesu, takich jak temperatura, ciśnienie, prędkość czy inne wartości krytyczne dla jakości produkcji. System zbiera dane w czasie rzeczywistym, porównując je z określonymi wartościami referencyjnymi, aby upewnić się, że proces przebiega zgodnie z założeniami technologicznymi.
Systemy MES wspierają również analizę statystyczną procesów, wykorzystując narzędzia takie jak SPC (Statistical Process Control). Pozwala to na identyfikację odchyleń od normy, szybkie wykrywanie potencjalnych problemów i wdrażanie działań korygujących. Dzięki temu możliwe jest utrzymanie stabilności procesów, minimalizacja strat i zapewnienie wysokiej jakości produktów.
12. Zarządzanie zamówieniami
System MES wspiera realizację zleceń produkcyjnych otrzymanych z systemu ERP, koncentrując się na operacyjnym monitorowaniu ich postępu. System śledzi status zleceń w czasie rzeczywistym, rejestruje zużycie materiałów, pracę maszyn i efektywność personelu. MES umożliwia także dynamiczne zarządzanie priorytetami zleceń, dostosowując kolejność realizacji do bieżących warunków na hali produkcyjnej. Dzięki temu wspiera terminowe dostawy i efektywne wykorzystanie zasobów, informując jednocześnie ERP o postępach w produkcji.
13. Zarządzanie magazynem
MES wspiera logistykę produkcyjną, koncentrując się na przepływie materiałów między magazynem a linią produkcyjną. Chociaż pełne zarządzanie stanami magazynowymi zazwyczaj odbywa się w systemach ERP lub WMS, MES rejestruje i monitoruje zużycie surowców oraz dostarczanie półproduktów i komponentów bezpośrednio do stanowisk produkcyjnych.
System pomaga również w synchronizacji dostaw materiałów z harmonogramem produkcji, minimalizując przestoje spowodowane ich brakiem. Informacje o aktualnym zapotrzebowaniu i wykorzystaniu są przekazywane do ERP lub WMS, co pozwala na precyzyjne zarządzanie zapasami i optymalizację kosztów.
14. Zarządzanie kosztami
MES gromadzi szczegółowe dane dotyczące kosztów produkcji, umożliwiając precyzyjne monitorowanie i analizę na każdym etapie procesu. System rejestruje kluczowe elementy kosztowe, takie jak zużycie materiałów, czas pracy maszyn i personelu, przestoje, odpady oraz energię. Dane te pozwalają na identyfikację obszarów generujących straty, takich jak niewykorzystany czas maszyn, wysokie wskaźniki braków czy nieefektywne wykorzystanie zasobów.
Rozwiązanie klasy MES wspiera optymalizację kosztów poprzez:
- Precyzyjne raportowanie – generowanie szczegółowych raportów dla poszczególnych zleceń, linii produkcyjnych lub etapów procesu.
- Identyfikację strat – wykrywanie źródeł marnotrawstwa, takich jak nadprodukcja, nadmiar surowców czy nadmierne zużycie energii.
- Analizę porównawczą – porównywanie kosztów dla różnych produktów, technologii czy zmian produkcyjnych w celu wyboru najbardziej opłacalnych rozwiązań.
Dzięki tym funkcjom MES umożliwia podejmowanie świadomych decyzji dotyczących poprawy efektywności kosztowej, takich jak optymalizacja harmonogramów, lepsze wykorzystanie zasobów czy redukcja odpadów. To wspiera osiąganie większej rentowności i konkurencyjności przedsiębiorstwa.
15. Zarządzanie utrzymaniem ruchu
Jednym z ważniejszych obszarów dla systemów MES jest wsparcie zarządzanie utrzymaniem ruchu, poprzez usprawnienie planowania, monitorowania oraz realizacji prac konserwacyjnych i naprawczych. W rezultacie minimalizuje ryzyko awarii oraz skraca czas przestojów. System pozwala na rejestrowanie przestojów w czasie rzeczywistym oraz automatyczne powiadamianie zespołów utrzymania ruchu, np. poprzez wiadomości na urządzenia mobilne. Dzięki temu proces naprawy może rozpocząć się natychmiast, co znacząco usprawnia czas reakcji i ogranicza straty wynikające z postoju maszyn.
MES często wspiera pełen proces zarządzania utrzymaniem ruchu, w tym:
- Monitorowanie czasu reakcji i naprawy poprzez rejestrację kluczowych parametrów, takie jak czas zgłoszenia, czas rozpoczęcia i zakończenia naprawy, co pozwala na analizę efektywności działań.
- Automatyczne powiązanie z danymi procesowymi – na podstawie odchyleń parametrów procesu lub alarmów generowanych przez maszyny system może automatycznie identyfikować awarie.
- Integracja z harmonogramem konserwacji dzięki możliwość planowania prac prewencyjnych na podstawie danych o stanie maszyn, takich jak liczba cykli czy czas pracy.
Niektóre systemy MES oferują funkcjonalności zbliżone do pełnych systemów klasy CMMS (Computerized Maintenance Management System), w tym zarządzanie harmonogramami konserwacji, zasobami do napraw czy historią działań serwisowych. Pozwala to na holistyczne zarządzanie utrzymaniem ruchu bez potrzeby dodatkowych narzędzi, zwiększając efektywność i niezawodność procesów produkcyjnych.
16. Zarządzanie zmianami produkcyjnymi
Systemy MES zapewniają kontrolę nad zmianami w procesach produkcyjnych, monitorując ich wpływ na efektywność, zgodność z wymaganiami i jakość. System dokumentuje wszystkie zmiany, takie jak wprowadzanie nowych wersji produktów, modyfikacje marszrut czy parametrów technologicznych, co pozwala na analizę ich wpływu na kluczowe wskaźniki, np. OEE (Overall Equipment Effectiveness). Dzięki temu możliwe jest badanie zależności między wersją produktu, marszrutą a wydajnością maszyn i personelu, co wspiera optymalizację procesów.
MES wspiera również pracowników w poprawnym wdrażaniu nowych produktów lub zmian w procesach, dostarczając listy kontrolne, instrukcje czy wytyczne na bieżąco. Przykładowo, przy zmianie produktu system może automatycznie wyświetlić operatorowi odpowiednie procedury czy dokumentację, eliminując ryzyko błędów i minimalizując czas potrzebny na adaptację.
Dzięki tym funkcjonalnościom MES ułatwia szybkie i skuteczne wdrażanie zmian, zapewniając jednocześnie ich zgodność z wymaganiami jakościowymi i regulacyjnymi oraz optymalizując wykorzystanie zasobów.
17. Zarządzanie bezpieczeństwem
System MES może wspierać monitorowanie procedur bezpieczeństwa i zapewnia zgodność z przepisami, co minimalizuje ryzyko wypadków i pomaga w utrzymaniu bezpiecznego środowiska pracy. System umożliwia rejestrowanie zdarzeń związanych z bezpieczeństwem, takich jak przestoje wynikające z zagrożeń czy niezgodności z normami, oraz wspiera analizę ich przyczyn w celu zapobiegania podobnym sytuacjom w przyszłości.
W celu egzekwowania zasad BHP MES może dostarczać listy kontrolne lub instrukcje dla pracowników, które muszą zostać wypełnione przed rozpoczęciem pracy na maszynach lub wdrożeniem określonych działań. Takie listy mogą obejmować m.in. weryfikację środków ochrony osobistej, sprawdzenie stanu urządzeń czy potwierdzenie przeszkolenia operatora. Dzięki temu MES wspiera przestrzeganie standardów bezpieczeństwa, a także dokumentuje ich realizację na potrzeby audytów i raportów zgodności.
17. Zarządzanie bezpieczeństwem
System MES może wspierać monitorowanie procedur bezpieczeństwa i zapewnia zgodność z przepisami, co minimalizuje ryzyko wypadków i pomaga w utrzymaniu bezpiecznego środowiska pracy. System umożliwia rejestrowanie zdarzeń związanych z bezpieczeństwem, takich jak przestoje wynikające z zagrożeń czy niezgodności z normami, oraz wspiera analizę ich przyczyn w celu zapobiegania podobnym sytuacjom w przyszłości.
W celu egzekwowania zasad BHP MES może dostarczać listy kontrolne lub instrukcje dla pracowników, które muszą zostać wypełnione przed rozpoczęciem pracy na maszynach lub wdrożeniem określonych działań. Takie listy mogą obejmować m.in. weryfikację środków ochrony osobistej, sprawdzenie stanu urządzeń czy potwierdzenie przeszkolenia operatora. Dzięki temu MES wspiera przestrzeganie standardów bezpieczeństwa, a także dokumentuje ich realizację na potrzeby audytów i raportów zgodności.
18. Raportowanie i analiza danych
Oprogramowanie MES zapewnia rozbudowane możliwości raportowania i analizy danych, wspierając zarówno bieżące działania operacyjne, jak i długoterminowe strategie. Dane w czasie rzeczywistym prezentowane są na dashboardach lub w systemach Andon, informując o kluczowych zdarzeniach, takich jak przestoje czy osiągnięcia wskaźników, co umożliwia natychmiastowe działania korygujące.
System oferuje również analizy porównawcze efektywności maszyn, linii produkcyjnych czy zmian roboczych, a także raporty i trendy w dłuższych horyzontach czasowych, wspierające planowanie i ocenę efektywności działań. Dla bardziej zaawansowanej analityki MES może integrować się z systemami BI, pozwalając na tworzenie niestandardowych raportów i wizualizacji. Dzięki temu MES wspiera zarówno codzienną optymalizację, jak i strategiczne decyzje zarządcze.
19. Zarządzanie energią
Oprogramowanie MES może monitorować zużycie energii przez maszyny i procesy, umożliwiając szczegółową analizę kosztów energetycznych, także na poziomie konkretnych zleceń produkcyjnych. Dane te pozwalają identyfikować energochłonne obszary i wdrażać działania optymalizacyjne. Dzięki temu możliwa jest redukcja kosztów i poprawa efektywności energetycznej.
20. Zarządzanie środowiskowe
System MES monitoruje zużycie zasobów, emisje i odpady, wspierając identyfikację energochłonnych procesów oraz zgodność z regulacjami. System pomaga optymalizować wykorzystanie zasobów i ograniczać wpływ na środowisko, wspierając realizację celów zrównoważonego rozwoju.
Zastosowanie oprogramowania MES w przedsiębiorstwach
Oprogramowanie MES (Manufacturing Execution System) znajduje zastosowanie w wielu branżach przemysłu, wspierając przedsiębiorstwa w optymalizacji procesów produkcyjnych. System sprawdza się zarówno w produkcji seryjnej, jak i jednostkowej, dostosowując się do specyficznych wymagań każdej branży.
Wpływ oprogramowania MES na efektywność i jakość produkcji
Oprogramowanie MES znacząco poprawia efektywność produkcji, monitorując procesy w czasie rzeczywistym i identyfikując wąskie gardła czy odchylenia. Śledzenie wskaźników takich jak OEE pozwala na eliminację strat i maksymalne wykorzystanie zasobów.
System umożliwia szybsze reagowanie na zmiany i redukcję kosztów operacyjnych.
MES wpływa także na jakość, monitorując kluczowe parametry procesów i wykrywając odchylenia, zanim wpłyną one na produkt końcowy. Narzędzia takie jak SPC pozwalają na analizę stabilności procesów, a pełna identyfikowalność (traceability) ułatwia kontrolę zgodności z wymaganiami.
Integracja z systemami ERP czy SCADA zapewnia spójność danych i lepsze decyzje biznesowe, a raporty i analizy generowane przez MES wspierają długoterminową optymalizację procesów i strategii produkcyjnych.
Oprogramowanie MES dla branży spożywczej
W branży spożywczej kluczowymi wyzwaniami są zapewnienie bezpieczeństwa żywności, spełnienie rygorystycznych wymogów regulacyjnych oraz zarządzanie krótkimi cyklami życia produktów. Oprogramowanie MES wspiera śledzenie partii (traceability), zarządzanie recepturami i kontrolę krytycznych parametrów procesów, takich jak temperatura czy wilgotność, zapewniając zgodność z normami HACCP i ISO. MES umożliwia także minimalizację strat surowców oraz optymalizację harmonogramów produkcyjnych, co pozwala na szybką reakcję na zmiany popytu i efektywne zarządzanie zasobami.
Oprogramowanie MES dla branży meblarskiej
Branża meblarska zmaga się z wyzwaniami związanymi z produkcją na zamówienie, różnorodnością asortymentu oraz optymalizacją wykorzystania materiałów. Oprogramowanie MES wspiera zarządzanie zleceniami produkcyjnymi, monitorowanie wydajności maszyn i kontrolę jakości na każdym etapie procesu. System umożliwia śledzenie materiałów, redukując odpady, oraz harmonogramowanie pracy, co pomaga efektywnie zarządzać dużą ilością małoseryjnych zamówień. MES integruje dane procesowe, wspierając szybką realizację zleceń i minimalizację kosztów produkcji.
Oprogramowanie MES dla branży automotive
Branża automotive charakteryzuje się wysokimi wymaganiami w zakresie jakości, identyfikowalności (traceability) i efektywności procesów. Oprogramowanie MES umożliwia śledzenie każdego etapu montażu, zarządzanie dostawami komponentów w modelu Just-in-Time oraz monitorowanie wskaźników takich jak OEE. System wspiera także zgodność z normami branżowymi, kontrolę jakości w czasie rzeczywistym oraz szybkie reagowanie na odchylenia, co minimalizuje ryzyko wad i kosztowne przestoje. MES pozwala również optymalizować złożone procesy logistyczne i produkcyjne, zwiększając wydajność w dynamicznym środowisku.
Oprogramowanie MES dla produkcji ogólnej
Produkcja ogólna wymaga elastyczności w zarządzaniu zróżnicowanymi zleceniami, optymalizacji procesów oraz kontroli jakości. Oprogramowanie MES pomaga monitorować realizację zleceń, śledzić zużycie materiałów i efektywność maszyn w czasie rzeczywistym. Dzięki funkcjom takim jak traceability, analiza wskaźników OEE czy dynamiczne harmonogramowanie, MES wspiera eliminację strat, zwiększenie wydajności oraz utrzymanie wysokiej jakości produktów. System integruje dane z maszyn i systemów zarządzania, ułatwiając podejmowanie lepszych decyzji operacyjnych i strategicznych.
Korzyści z wdrożenia systemu MES
Wdrożenie systemu MES (Manufacturing Execution System) przynosi przedsiębiorstwom znaczące korzyści w obszarach wydajności, jakości oraz redukcji kosztów.
Na stronach wielu producentów systemów klasy MES możemy znaleźć deklaracje i obietnice osiągnięcia znaczących efektów, jak np. redukcja czasu cykli o 35%, obniżenie kosztu magazynu o ponad 20% czy skrócenie Lead Time o połowę. W naszej praktyce skala osiągniętych efektów zależy od wielu czynników. Zapewne, dla wielu firm produkcyjnych takie wielkości są osiągalne, dla innych natomiast – podniesienie efektywności produkcji nawet o 3-4% będzie ogromną korzyścią która zapewni ekspresowy zwrot z inwestycji w MES.
Najważniejsze korzyści które można osiągnąć wdrażając system klasy MES (według badań MESA International i innych niezależnych źródeł), to:
- Zwiększenie wydajności produkcji, która w rezultacie wdrożeń często poprawia się o ponad 5%, dzięki lepszemu zarządzaniu procesami i redukcji przestojów.
- Redukcja czasów cyklu produkcyjnego/lead time co umożliwia szybszą realizację zamówień.
- Ograniczenie czasów nieprodukcyjnych – skrócenie przestojów i eliminacja marnotrawstwa poprzez automatyzację zgłoszeń i monitorowanie w czasie rzeczywistym.
- Usprawnienie komunikacji dzięki informacji o statusie produkcji dostępnej w czasie niemal rzeczywistym dla wszystkich działów przedsiębiorstwa.
- Redukcja kosztów związanych z dystrybucją zadań dzięki eliminacji papierowych instrukcji i raportów.
- Poprawa jakości produktów dzięki zmniejszeniu liczby wadliwych wyrobów.
- Redukcja kosztów wprowadzania i agregacji danych dotyczących realizacji produkcji, jak również minimalizacja błędów ludzkich.
- Obniżenie poziomu zapasów dzięki efektywnemu planowaniu i monitorowaniu wykorzystania materiałów.
- Utrwalenie wiedzy eksperckiej, posiadanej często przez najbardziej doświadczonych pracowników poprzez gromadzenie danych procesowych i dostarczanie pracownikom dokumentacji.
- Możliwość zdalnego zarządzania produkcją – MES umożliwia monitorowanie i zarządzanie procesami na odległość, wspierając elastyczność i szybką reakcję.
- Umożliwienie stworzenia uczciwego systemu premiowania – dane z systemu MES pozwalają rzetelnie ocenić efektywność i wyniki poszczególnych pracowników.
- Podniesienie motywacji i zaangażowania pracowników poprzez jasny podgląd wyników, automatyczne rozliczanie pracy.
- Jeden, spójny obraz procesu produkcyjnego dostępny w czasie rzeczywistym wspiera lepsze decyzje na każdym poziomie organizacji a w rezultacie pomaga w integracji wszystkich działów przedsiębiorstwa.
Podsumowując – system klasy MES to narzędzie, które nie tylko poprawia operacyjne aspekty produkcji, ale także wspiera długoterminowy rozwój organizacji, integrując kluczowe procesy i wspierając lepszą współpracę między działami.
Zwrot z inwestycji w system MES (Return on Investment)
Zwrot z inwestycji (ROI) w projekt wdrożenia systemu klasy MES to bardzo ważny czynnik decydujący o jego rozpoczęciu. W naszej praktyce wdrożenie systemu MES często przynosi szybki zwrot z inwestycji, który można osiągnąć już w 6 miesięcy od uruchomienia produkcyjnego. Dzięki redukcji przestojów, skróceniu czasu reakcji, poprawie jakości i efektywniejszemu wykorzystaniu zasobów przedsiębiorstwa odnotowują znaczące oszczędności operacyjne. Szybkie korzyści wynikają również z lepszej kontroli nad procesami, mniejszej liczby odpadów oraz optymalizacji czasu pracy i zużycia materiałów. Wysoki poziom integracji i elastyczność systemu MES sprawiają, że inwestycja w to rozwiązanie zaczyna się zwracać w niezwykle krótkim czasie, w porównaniu do innych rozwiązań IT wykorzystywanych w firmach produkcyjnych.
Integracja systemu MES z innymi systemami
Integracja systemu MES (Manufacturing Execution System) z innymi systemami w przedsiębiorstwie, takimi jak ERP, WMS, CMMS, APS czy nawet arkuszami kalkulacyjnymi Excel (często nazywanymi żartobliwie “najpopularniejszym systemem zarządzania produkcją na świecie”), jest kluczowa dla pełnego wykorzystania możliwości systemu MES. Integracja pozwala uzyskać spójne środowisko informacyjne, umożliwiające efektywną wymianę danych i optymalizację procesów na wszystkich poziomach organizacji.
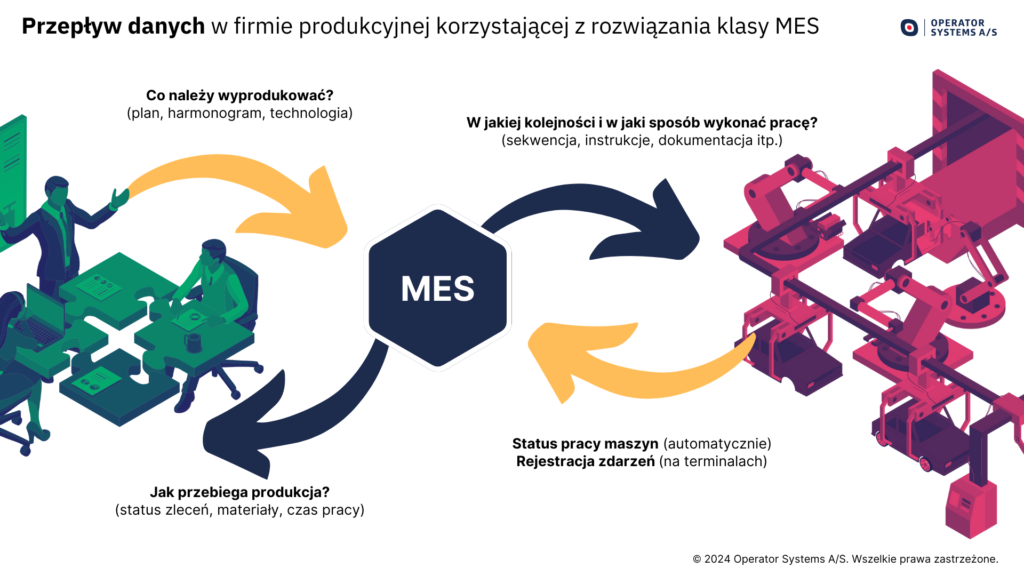
Integracja systemu MES z innymi systemami
Połączenie z systemem ERP (Enterprise Resource Planning) umożliwia synchronizację danych dotyczących zamówień, planów produkcyjnych oraz stanów magazynowych. Informacje o zużyciu materiałów i produkcji wyrobów gotowych są aktualizowane na bieżąco, co wspomaga zarządzanie zasobami i kontrolę finansową produkcji. Integracja z ERP jest zazwyczaj dwukierunkowa, a popularnymi metodami wymiany danych są połączenia baza-baza czy interfejsy REST API.
Integracja z systemem WMS (Warehouse Management System) pozwala na efektywne zarządzanie logistyką wewnętrzną poprzez synchronizację przepływu materiałów między magazynem a produkcją. System MES informuje WMS o zapotrzebowaniu na materiały i odbiorze wyrobów gotowych, co usprawnia procesy magazynowe i minimalizuje opóźnienia.
Połączenie z systemem CMMS (Computerized Maintenance Management System) wspomaga utrzymanie ruchu, umożliwiając planowanie prac konserwacyjnych i monitorowanie stanu maszyn. Dane o awariach i potrzebach serwisowych są wymieniane między systemami, co zwiększa niezawodność sprzętu i redukuje nieplanowane przestoje.
System APS (Advanced Planning and Scheduling) zajmuje się zaawansowanym planowaniem i harmonogramowaniem produkcji. Integracja MES z APS pozwala na dynamiczne dostosowywanie planów produkcyjnych w oparciu o aktualne dane dotyczące dostępności zasobów i obciążenia maszyn. Wymiana informacji odbywa się zazwyczaj dwukierunkowo przy użyciu interfejsów API lub bezpośrednich połączeń baz danych.
Niezmiennie popularnym źródłem danych są także wspomniane arkusze kalkulacyjne, tworzone przy użyciu narzędzi takich jak Microsoft Excel. Integracja MES z takimi narzędziami umożliwia importowanie i eksportowanie informacji, co ułatwia analizę i raportowanie bez konieczności ręcznego wprowadzania danych i często jest rekomendowana na etapie projektów pilotażowych czy tzw. Proof-of-Concept.
Akwizycja danych z maszyn
Aby rozwiązanie klasy MES mogło efektywnie monitorować procesy na hali produkcyjnej, konieczne może się okazać pozyskiwanie danych bezpośrednio z maszyn. Można to zrealizować na wiele sposobów, wykorzystując w tym celu protokoły takie jak OPC/OPC UA czy MQTT, które umożliwiają niezawodny i bezpieczny transfer danych.
Akwizycja danych z maszyn jest zazwyczaj jednokierunkowa – system MES odczytuje informacje o stanie maszyn, parametrach procesu czy występujących alarmach, ale nie ingeruje w sterowanie samym procesem. Taki model zapewnia bezpieczeństwo operacyjne i pozwala uniknąć niepożądanych zmian w działaniu urządzeń, koncentrując się na monitorowaniu i analizie danych produkcyjnych.
Dzięki pozyskiwaniu danych z maszyn, MES może na bieżąco śledzić wydajność produkcji, wykrywać anomalie i wspierać działania mające na celu optymalizację procesów. Integracja na tym poziomie jest kluczowa dla osiągnięcia pełnej transparentności i efektywności w zarządzaniu produkcją.
Znaczenie integracji dla optymalnego wdrożenia MES
Pełna integracja MES z innymi systemami oraz z maszynami na hali produkcyjnej jest niezbędna dla osiągnięcia spójności danych i efektywności operacyjnej. Umożliwia to automatyzację procesów, szybszy przepływ informacji i lepszą komunikację między różnymi działami przedsiębiorstwa. Wykorzystanie odpowiednich protokołów i interfejsów, takich jak baza-baza, REST API, OPC/OPC UA czy MQTT, zapewnia niezawodną i bezpieczną wymianę danych.
Integracja systemów przygotowuje również firmę na przyszłe wyzwania związane z cyfryzacją i automatyzacją produkcji, zgodnie z ideą Przemysłu 4.0. Odpowiednio wdrożony system MES staje się wówczas nie tylko narzędziem operacyjnym, ale strategicznym elementem wspierającym rozwój i konkurencyjność przedsiębiorstwa.
Przyszłość systemów MES
Systemy MES (Manufacturing Execution Systems) nieustannie się rozwijają, dostosowując do zmieniających się potrzeb i wymagań przemysłu. Choć koncepcje takie jak Przemysł 4.0 czy Internet Rzeczy (IoT) bywają trudne do jednoznacznego zdefiniowania i czasem postrzegane są jako „modne hasła”, odzwierciedlają one realne trendy technologiczne i oczekiwania rynku. Zrównoważony rozwój, efektywność energetyczna, gospodarka o obiegu zamkniętym oraz wyzwania związane z rozwojem kadr i lukami kompetencyjnymi wpływają na kierunek ewolucji systemów MES. Według naszej obecnej wiedzy, istnieje kilka wyraźnych kierunków tej ewolucji:
- Wykorzystanie AI i uczenia maszynowego – Systemy MES będą w coraz szerszym zakresie korzystać ze sztucznej inteligencji do analizy danych produkcyjnych, co pozwoli na przewidywanie awarii, optymalizację harmonogramów oraz automatyczne dostosowywanie parametrów produkcji w celu minimalizacji zużycia energii i materiałów.
- Zrównoważony rozwój i efektywność energetyczna – MES odegra kluczową rolę w monitorowaniu i redukcji zużycia energii oraz emisji, umożliwiając przedsiębiorstwom osiągnięcie celów związanych ze zrównoważonym rozwojem poprzez optymalizację procesów pod kątem ekologii i ekonomii.
- Wsparcie dla gospodarki o obiegu zamkniętym – Systemy MES będą integrować się z procesami recyklingu i ponownego wykorzystania materiałów, umożliwiając śledzenie surowców na każdym etapie cyklu życia produktu i wspierając inicjatywy związane z gospodarką o obiegu zamkniętym.
- Integracja z IIoT – MES będzie coraz bardziej łączył się z urządzeniami IIoT, co umożliwi szczegółowe monitorowanie procesów produkcyjnych i szybsze reagowanie na zmiany. Sensory i inteligentne urządzenia dostarczą danych nie tylko o wydajności, ale także o zużyciu energii i wpływie na środowisko.
- Rozwój kadr i eliminacja luk kompetencyjnych – Wraz z wprowadzaniem nowych technologii pojawia się potrzeba ciągłego szkolenia pracowników. Systemy MES mogą wspierać ten proces poprzez dostarczanie instrukcji pracy, monitorowanie poprawności realizacji zadań czy rozwój kompetencji, co pomoże w eliminacji luk kompetencyjnych.
- Zwiększone znaczenie cyberbezpieczeństwa – W miarę wzrostu liczby połączonych urządzeń i systemów, zabezpieczenie danych i infrastruktury staje się priorytetem. MES będzie musiał spełniać najwyższe standardy bezpieczeństwa, aby chronić przedsiębiorstwo przed potencjalnymi zagrożeniami.
- Interoperacyjność i otwarte standardy – MES będzie musiał współpracować z różnymi systemami i urządzeniami, dlatego stosowanie otwartych standardów komunikacyjnych i protokołów stanie się niezbędne. Ułatwi to integrację i wymianę danych między różnymi elementami ekosystemu przemysłowego, wspierając inicjatywy zrównoważonego rozwoju.
- Chmura obliczeniowa i edge computing – Przeniesienie części funkcjonalności MES do chmury ułatwi dostęp do danych i skalowalność systemów, podczas gdy edge computing pozwoli na przetwarzanie danych bezpośrednio na urządzeniach, co jest istotne dla szybkiego reagowania i redukcji zużycia energii.
Podsumowując, w obliczu ciągłych zmian technologicznych i rosnących wymagań rynku, ewolucja systemów MES jest niezbędna. Wybierając rozwiązanie klasy MES, warto zwrócić uwagę na jego zdolność do adaptacji i przygotowanie na przyszłe wyzwania. Inwestycja w elastyczny system zapewni firmie możliwość skutecznego reagowania na zmiany i utrzymania przewagi konkurencyjnej.
Jeżeli chcesz dowiedzieć się, jak w Operator Systems planujemy odpowiedzieć na te wyzwania skontaktuj się z nami, chętnie podzielimy się naszym planem rozwoju na najbliższe lata.
Ile kosztuje wdrożenie systemu MES?
Koszt wdrożenia systemu MES może znacznie się różnić w zależności od wielu czynników. Nie ma jednej uniwersalnej ceny, ponieważ każdy projekt jest unikalny i dostosowany do specyficznych potrzeb przedsiębiorstwa. W Operator Systems jesteśmy w stanie wskazać przybliżony koszt wdrożenia już po pierwszym spotkaniu, gdzie wspólnie ustalimy jaki zakres i skala wdrożenia będzie właściwa dla Twojej produkcji. Jeśli interesuje Cię taka wycena skorzystaj z formularz kontaktowego i umówmy się na spotkanie. Jeśli natomiast chcesz poznać orientacyjny koszt wdrożenia systemu klasy MES, poniżej znajdziesz przykładowe liczby:
- Mała firma produkcyjna (50 osób na produkcji), podstawowe funkcjonalności systemu, integracja z jednym systemem nadrzędnym (np. ERP) – 150 000 PLN – 300 000 PLN.
- Większa firma produkcyjna (50-150 osób na produkcji), dodatkowe moduły (np. Kontrola Jakości, Logistyka Produkcyjna), bardziej złożona integracja – 250 000 PLN – 600 000 PLN.
- Duża firma produkcyjna (150+ osób na produkcji), szeroki zakres funkcjonalny, złożone integracje z wieloma systemami, dodatkowe dedykowane funkcjonalności – 500 000 PLN+.
Powyższe wartości przedstawiają orientacyjny koszt licencji oraz usługi wdrożenia systemu. Należy jednak mieć na uwadze, że na całkowity koszt wdrożenia systemu MES składa się znacznie więcej czynników, których kompletną listę przedstawiamy poniżej.
Licencje, wdrożenie i utrzymanie od dostawcy systemu
- Licencje na oprogramowanie – opłaty za korzystanie z systemu MES, które mogą być jednorazowe lub abonamentowe.
- Usługi wdrożeniowe – koszty związane z instalacją, konfiguracją i dostosowaniem systemu do specyficznych potrzeb firmy.
- Utrzymanie i wsparcie techniczne – opłaty za aktualizacje oprogramowania, pomoc techniczną oraz ewentualne rozszerzenia funkcjonalności.
Wsparcie specjalistów i integratorów
- Dostawcy maszyn i systemów (np. ERP) – koszty związane z zaangażowaniem ekspertów, którzy pomogą w integracji MES z istniejącymi systemami i maszynami.
- Integratorzy systemów – firmy lub specjaliści odpowiedzialni za koordynację procesu integracji, zapewniający sprawną komunikację między różnymi systemami.
System akwizycji danych
- Czujniki i urządzenia pomiarowe – inwestycja w sprzęt potrzebny do zbierania danych z maszyn i procesów produkcyjnych.
- Komputery edge i infrastruktura IT – zakup dodatkowych urządzeń do przetwarzania danych na poziomie lokalnym, co zwiększa efektywność i szybkość reakcji systemu.
- Terminale dla pracowników – wyposażenie stanowisk pracy w urządzenia umożliwiające interakcję z systemem MES, takie jak tablety czy ekrany dotykowe.
- Urządzenia mobilne – potrzebne dla np. pracowników utrzymania ruchu czy kontrolerów jakości prowadzących inspekcję materiałów przychodzących.
Czas i wysiłek organizacyjny
- Zaangażowanie personelu – czas pracowników poświęcony na planowanie, testowanie i wdrażanie systemu.
- Szkolenia – koszty związane z edukacją personelu w zakresie obsługi nowego systemu i procedur.
- Adaptacja procesów – Konieczność dostosowania istniejących procesów biznesowych do nowego systemu, co może wymagać dodatkowych nakładów pracy.
Dodatkowe czynniki
- Skala wdrożenia – wielkość przedsiębiorstwa i zakres implementacji wpływają na ogólne koszty projektu.
- Specyficzne wymagania branżowe – branże o wysokich standardach regulacyjnych mogą wymagać dodatkowych funkcjonalności, co zwiększa koszt.
Wdrożenie systemu MES to kompleksowy proces, który wymaga uwzględnienia wielu czynników wpływających na całkowity koszt. Obejmuje to nie tylko bezpośrednie wydatki na licencje i usługi dostawcy, ale także inwestycje w sprzęt, integracje, szkolenia oraz czas i zaangażowanie zespołu. Dlatego ważne jest, aby przed podjęciem decyzji dokładnie przeanalizować potrzeby przedsiębiorstwa, dostępne zasoby oraz potencjalne korzyści płynące z wdrożenia systemu MES. Tylko wtedy inwestycja ta przyniesie oczekiwane rezultaty i przyczyni się do poprawy efektywności oraz konkurencyjności firmy.
System MES - Podsumowanie
System MES (Manufacturing Execution System) to kluczowe narzędzie wspierające nowoczesne firmy w zarządzanie produkcją. Umożliwia monitorowanie, kontrolę i optymalizację procesów produkcyjnych, integrując się z innymi systemami i pobierając dane z maszyn. Rozwiązania MES pozwalają uzyskać pełną transparentność działań, podnieść efektywność i sprawnie reagować na zmieniające się warunki rynkowe.
Wdrożenie systemu MES to złożony proces – w zależności od specyfiki projektu może trwać od 3 miesięcy do nawet ponad roku. Natomiast rozwój takiego rozwiązania w praktyce się nie kończy. Dostosowywanie do zmian, wprowadzanie usprawnień, rozszerzanie na kolejne maszyny czy uruchamianie dodatkowych modułów – to możliwości, które daje współpraca ze sprawdzonym dostawcą.
Decyzja o wdrożeniu systemu MES wiąże się z wieloma pytaniami i wątpliwościami. Dlatego zachęcamy do dalszego zgłębiania tematu i skontaktowania się z nami w celu omówienia szczegółów. Dostarczamy systemy klasy MES od ponad 20 lat i chętnie podzielimy się naszymi doświadczeniami z projektów, jak również przygotujemy koncepcję wdrożenia która uwzględni specyfikę, skalę oraz budżet Twojej produkcji.